Avoid Pallet Racking Failure with QTS Products
For warehouses, the soundness of pallet racking systems isn’t just a matter of efficiency – it’s a matter of safety. Here’s how you can avoid the common pitfalls of pallet racking failures, leveraging the innovative solutions provided by QTS products.
Contents
Forklift Accidents: A Collision Course with Risk
The result of a forklift (or other MHE) colliding with the pallet racking can be catastrophic to both operatives and business operations. It is one of the most common causes of pallet racking failure and your customers can easily reduce risk through some preventative investment.
The solution:
There are 2 main solutions for this kind of accident. Firstly, it is important to ensure that your warehouse operatives are properly qualified to operate the forklifts. We aren’t experts on this though, so check out the HSE website for more information.
The second solution your customers could employ is some physical barriers to prevent a direct collision with the racking uprights. Our new rackPROTECT range is perfect for this. This range includes End-of-Aisle Rack Protectors, Pallet Racking Upright Protectors, and Rack Deflectors, each designed to shield racking components from operational impacts.
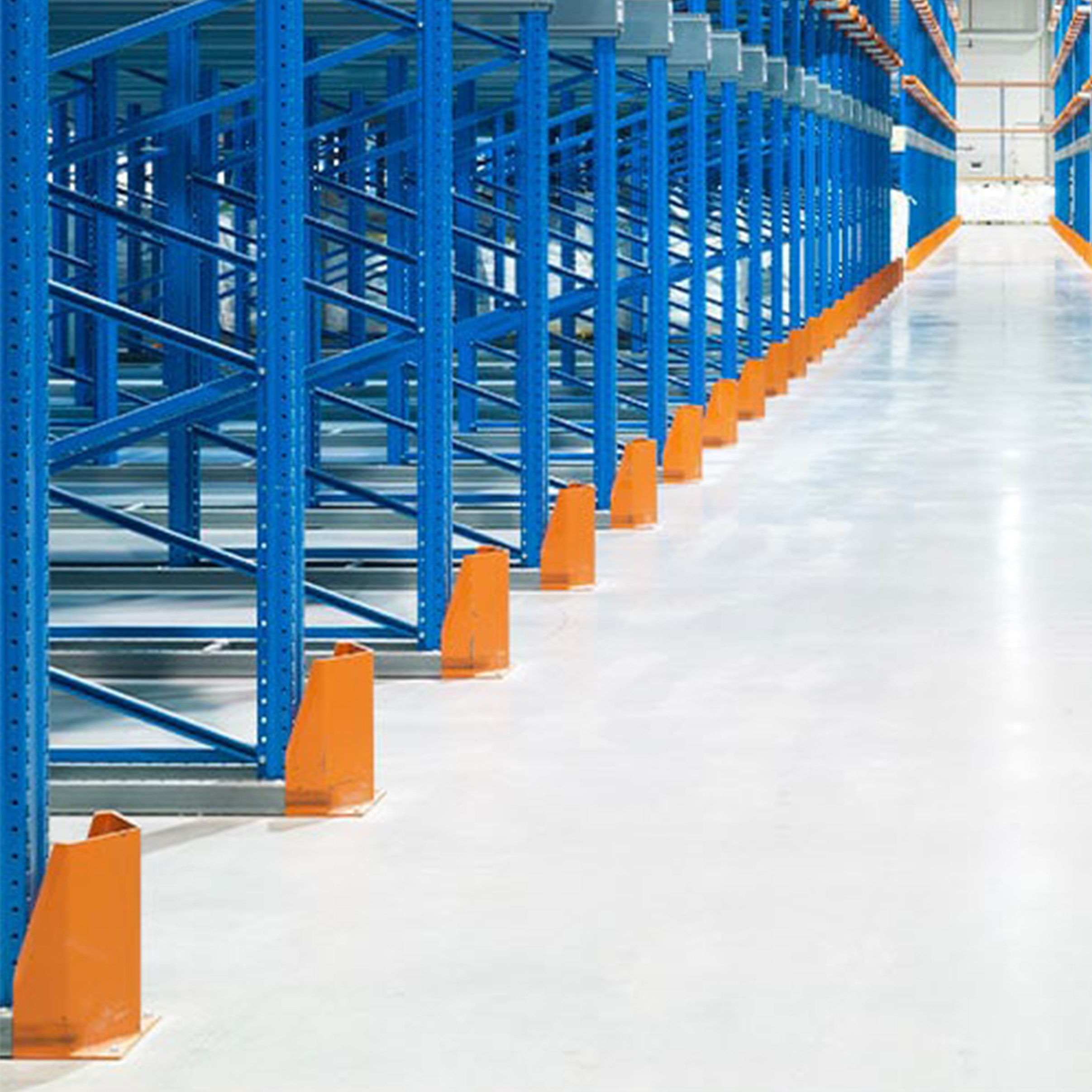
Inaccurate Bay Loading: Precarious Positioning
Incorrectly loading pallets in a storage bay might seem like a minor oversight, but its consequences can be significant. When a pallet isn’t seated correctly within its designated spot, the odds of it falling drastically increase.
The solution:
To begin with, it is good practice for your racking bays to have some kind of shelf which reduces the margin of error for loading and loading. One such solution from QTS is the easySHELF™ wire mesh deck which comes in many forms to suit your customer’s specific requirements.
Secondly, adding protection at the back of your racking prevents pallets or items falling off of the back of the racking if they have not been positioned properly. QTS’s rackGUARDIAN™ anti-collapse mesh is a high-strength screen made up of steel panels that prevent such accidents by providing a physical barrier.
Poor Warehouse Design
The design phase of a warehouse is imperative to its safety and functionality. A frequent error is failing to provide sufficient space between the aisles.
This means it is a tight squeeze for warehouse operators to move pallets through the aisle, increasing the likelihood of collision with the racking. It can also make it difficult for them to load and unload the racking system.
The solution:
The solution is to know exactly what your customer will be storing and how the load will be distributed over the bay. There are multiple types of racking systems available that can make the most of the available space but of course, some are not suited to heavier items or have a large upfront cost.
Overloading: A Weighty Issue
Wire mesh decks, while sturdy, have limits. Overloading them or placing items unevenly can strain the system.
The solution:
Similar to the previous example, planning is key when it comes to weight loading. It is important to plan what is going to be stored on each level and comply with the load notices that are on the bay. If the decks are not capable of taking that weight then new decks should be ordered to ensure the safety of the stored goods.
Securing the Future with QTS Products
The integrity of your warehouse’s pallet racking systems is non-negotiable. As the above issues highlight, many factors can compromise this integrity. But with foresight, vigilance, and the right products, these challenges can be overcome.
Are you ready to fortify your warehouse operations?
Share This: